Case Study
Rail Infrastructure Division of a Multinational Infrastructure Business – Business Improvement Project
I was asked to review the Australian Rail Infrastructure Division of Multinational Infrastructure Business as it was making a $200k loss from $30M of external revenue and $5M of internal revenue.
The initial requirement was for a high-level review of the business, with the results to be reported back to the Senior Management Team on day 8, as to whether the Rail Infrastructure Division could and should be saved or divested.
Initial investigations included team meetings, a financial review, individual meetings, research and a review of the business’s policies and procedures.
The review highlighted a number of poor practices including:
- Inaccurate financial reporting.
- Key personnel not following company policies and procedures.
- Lack of understanding of internal systems.
- Lack of training.
Concentrating on the key profit areas, I identified the following major issues and savings from corrections:
- Machine movements across the country had an annual cost of $12.5M. Investigations identified that contracts were being given to one supplier without obtaining a minimum of three quotes as per company policy. The result of obtaining three quotes highlighted a 40 to 50% drop in quotes from the most expensive to least expensive quote. The most expensive quote was 40% less than what was currently being paid plus offered a premium service with guaranteed delivery dates which was not offered by the original supplier. Net savings $5.0m
- A review of the costing models showed that staff were being charged out at their base rate plus 25% markup. A review of employee contracts and payroll reports showed:
- The maximum staff productivity from a 40-hour week after deducting annual leave, public holidays, technical training, health & safety training, site inductions, sick leave, bereavement leave, etc was just under 50%.
- On average each employee was doing an additional 40 hours per week of overtime of which, being in Australia, the first 3 hours per week were at time-and-a-half and the remainder at double-time.
- Employees are paid both out-of-state and mining allowances if working on a mining site, neither of which were included in the charge rate. 75% of work was out of state and 50%+ at mining sites.
- No cost of capital, management or office overheads were included in the costing model.
The Division’s clients had commented that the Division’s rates were significantly cheaper than the next cheapest quote, which should have been an indication of issues with the costing model.
- The Division’s Management was looking to reduce staffing to cut costs. After a brief discussion with the Division’s Management Team, it was decided that it was actually much more cost effective to increase staffing levels which would then reduce the levels of overtime plus avoid any potential fatigue claims from tired overworked employees.
- Updated financial management reports to give the business a better understanding of what was actually happening in their business. This included correct capacity and revenue reporting.
As the above contained $10M in profit improvement it was decided to go ahead with the improvements and keep the Division. My contract was extended to implement the improvements / changes plus identify any additional improvements.
The net result of this project was a $12M improvement in the business and a change to most of the Division’s Management Team.
For more information on what help I can provide call John Raffaelli on (021) 625-871 or alternatively go to our website by clicking here https://intotheblue.co.nz
For more information on creating or improving a business model please call John on (021) 625-871, and further more information please visit Into the Blue.
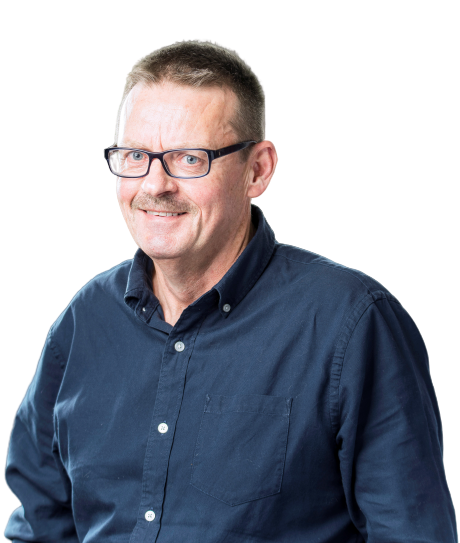