Case Study
Manufacturing Company – Business & Process Improvement Project
I was asked by a niche Cheese Manufacturer, which was part of a larger dairy company, to provide cover for their Management Accountant position as the existing Management Accountant was retiring. The Cheese Manufacturer had a new General Manager who thought the business’s gross margins were not only too low but also too variable, and so wanted a seasoned professional to come in and make any required improvements prior to recruiting a replacement Management Accountant.
The General Manager initially wanted:
- Documented processes of the Management Accountant’s position.
- A review and update of all costing models and costing processes.
- A review and update of all Bill of Materials (BOMs) and BOM processes.
- Complete the Management Accountant duties until the position was filled.
I had a one-day handover from the retiring Management Accountant on how to perform the requirements of his position.
During my review and writing of the positions processes I identified the following gross margin issues:
- The Cheese Manufacturer purchased milk from both Fonterra and independent dairy farmers. While they were both paid the same price for the milk, no account had been taken of the milk tanker freight costs. This highlighted the following issues:
- Fonterra tankers were delivered full.
- Independent tankers were delivered at no more than 50% full.
- Approximately 50% of the milk came from independent dairy farms.
- The freight cost for a part-filled tanker was the same as a full tanker.
- The delivery cost of a full Fonterra tanker was approximately 33% of the total cost of the purchase of the full tanker vs 50%+ of delivering from an independent dairy farm.
- Owing to potential health and traceability issues a milk tanker was not allowed to pick up from more than one dairy farm at a time.
- Costing models were based on full milk tankers.
- The Cheese Manufacturer used a local subcontractor to contract manufacture a couple of varieties of cheese. This highlighted further issues:
- The Cheese Manufacturer was providing the milk to the Contract Manufacturer but not charging the Contract Manufacturer for the milk.
- The Contract Manufacturer charged the Cheese Manufacturer for the cheese at its cost, to produce the cheese plus a margin.
- The costing model for contract manufactured cheese was based on the Contract Manufacturer’s price and sold based on that price plus a margin. No milk price included in the model.
A meeting with the new General Manager and Management Team concluded with:
- Cancellation of all independent dairy farm milk producers’ contracts unless they could guarantee full milk tankers.
- Contract Manufacturer to be charged for milk and freight so that all costs were included in the costings to determine the sale price of the cheese.
The net result of these changes was increased and stable gross margins. The new gross margins also reflected those calculated in the costing models and Bill of Materials.
For more information on what help I can provide call John Raffaelli on (021) 625-871 or alternatively go to our website by clicking here https://intotheblue.co.nz
For more information on creating or improving a business model please call John on (021) 625-871, and further more information please visit Into the Blue.
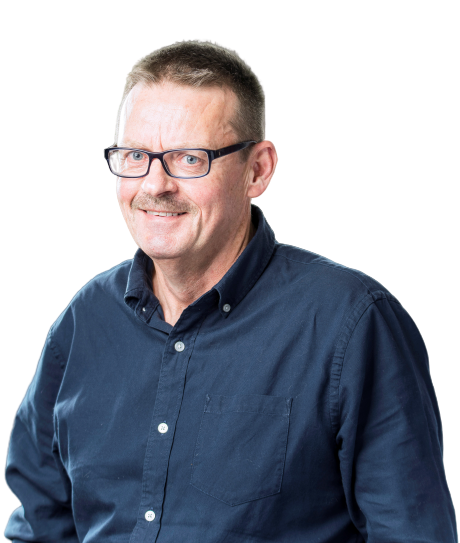